
EIGHTY PERCENT CLEARANCE BY 20:00
Client: Distribution Company Stamford, CT Facility
Services
Business Process Improvement Consulting
Manufacturing Continuous Process Improvement Consulting
Problem/Objectives
By performance standards the facility needed 80 percent of their products to clear their initial sorting process by 8 pm 6 nights a week. This particular facility in Stamford was only clearing at a rate of 36 percent. This late clearance was causing a ripple effect, with untimely products in the network, under utilized transportation, and increased cost in extra transportation.
Solution
-
Start reporting how much product has been cleared on an hourly basis starting at 4 pm
-
Increase the amount of product available for processing earlier in the processing window
-
Change the transportation schedule for the local distributors that provided the highest volume of product to the facility daily
-
Eliminate all bottlenecks within the facility to improve the flow of products moving through the facility
At a Glance
The distribution company had a set of key performance indicators that were measured over a 24 hour period. These indicators were used to measure and predict the success of each facility’s process at ensuring that their products were successful making assigned transportation within the distribution network. This particular facility was failing getting product through the network timely. One indicator, in particular, stood out as a dramatic failure for the facility. This failure was thought to be the cause for the facilities failures.
Our approach was to integrate with management and key personnel within the facility in order to understand operational processes. We put together a working group. We then mapped the entire process from beginning to end, so that we may understand current state. The team spent time walking through the process steps, conducting time studies, identifying roadblocks, and interviewing employees involved with the process.
Once all the information was compiled and analyzed, working together with the internal working group, we were able to develop a course of action. Our primary objective was to increase the volume of product clearing the process by the scheduled time. First, we increased the speed and efficiency of the process. This allowed the products to navigate through facility at a faster pace. This gave the facility the opportunity to take on move volume earlier in the day. Next, we increased the amount coming into the facility prior to 6 pm. By doing this we were able to eliminate any slowed down operational periods, that were due to the lack of volume created as a result of the newfound efficiency in the clearance process.
Results
Cost Savings – 500K/yr Transportation Costs
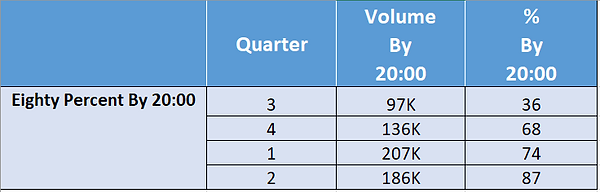